
Redesign of a Training Product
THE PROBLEM
Background
Organizations wishing to improve business processes and customer value demand Lean Six Sigma certification. Training and certification at the Yellow Belt level can be the precursor to more advanced training. The following case study is about an organization that took its in-classroom Yellow Belt program in a new direction by improving retention and performance on the job and making the training accessible for remote workers and online.
Problem to be Solved and Goals
​
A post-training analysis of a classroom-based, Lean Six Sigma Yellow Belt program revealed after 30 days provided insights to the researcher and instructor of what needed to be improved. It was clear from this analysis of 64 responders that tool usage (seven of them) didn't get traction as anticipated. The improvement goals are as follows:
Improve the classroom-based Lean Six Sigma Yellow Belt program to achieve the following goals:
-
Introduce "scientific thinking" to employees to enhance data acumen skills
-
Improve retention over time of the fundamental principles
-
Observe more Lean Six Sigma tool use at the point of work
-
Make it accessible to remote workers.
Duration of Project
Two Months
Participants
70 employees
Tools
Adobe Photoshop, Microsoft SharePoint, and Survey Monkey

Prototyping for Usability and Agility
Each session of the Yellow Belt training was considered a minimal viable product (MVP). Feedback was provided by each participant using card sorting or green card/red card feedback.
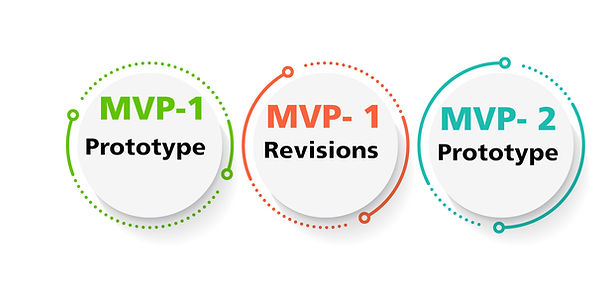
Card Sorting
Was used during the live sessions by users to provide feedback on what was working and what could be improved. The researcher captured and clustered comments for review.


Information
Architecture
The MOOC or Massive Open Online Course, required an outline or wireframe all the components to understand the user's flow through the MOOC.


Sample interface of the MOOC build in Microsoft SharePoint - Sample Interface
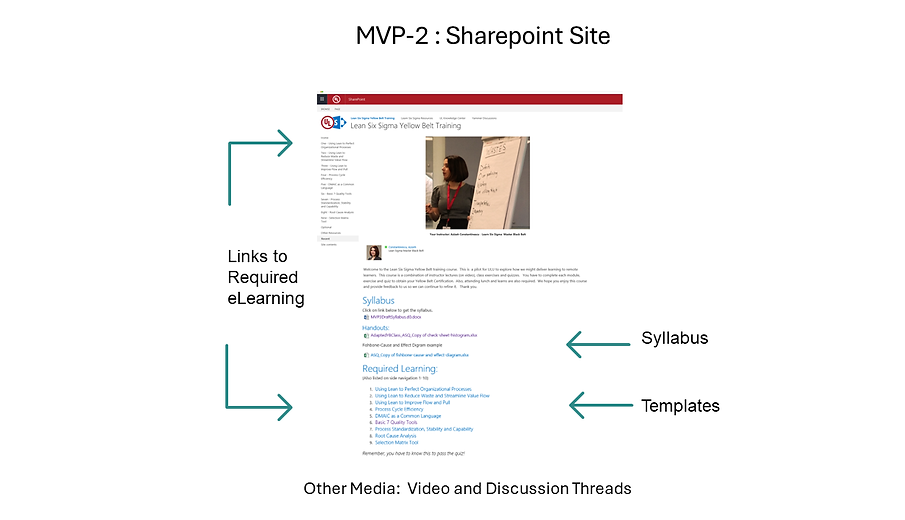
Comparison to the original Yellow Belt course and the new online version

Results
-
Reduced content to learn more appropriate content from 37 Lean Six Sigma tools to six tools.
-
Applied DMAIC (Define, Measure, Analysis, Improve, and Control) instead of theoretical concepts.
-
The company now had a learning solution to reach the remote workers, which was important during COVID-19.
-
Before going virtual, hotel and travel costs were associated with 20-30 percent of the employees who had to travel to the training site. The online training eliminated that expense.
-
Most importantly, post-survey data shows an increase in employees using the seven tools. This is a real benefit to the organization, as people practice new skills daily.

Reflection

Reflection
Initially, a post-training survey revealed the need to improve and our concern about reaching remote learners. Even weeks and months after the training, we were curious. That curiosity paid off.
​
The Lean Six Sigma Yellow Belt training program continues and has taught hundreds of employees worldwide. The course is also continuously improving.
The Lean Six Sigma Yellow Belt program is learning about "product." It is consumed by people and, like any product, deserves attention to the user's experience. We did that and continue to do it in all the products we design and implement for people.